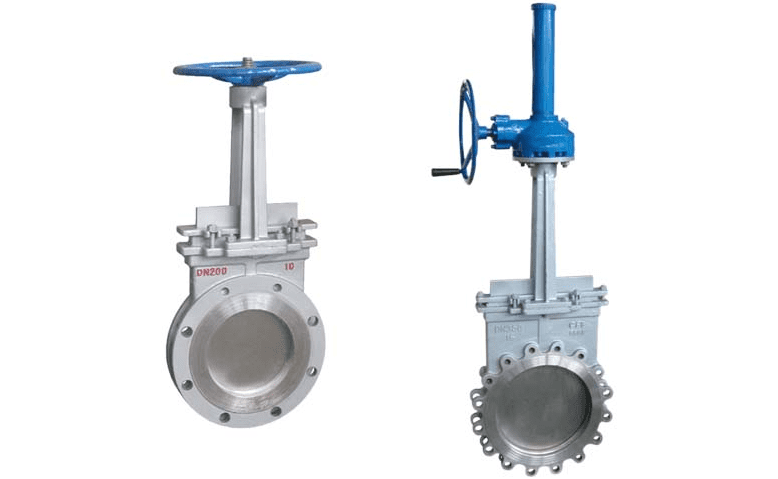
Are you in the market for a valve that can handle tough industrial applications? Look no further than the knife gate valve. These valves are designed to precisely control the flow of liquids or gases, making them an essential tool for many industries. But what exactly is a knife gate valve? And how do you choose the right one for your needs? In this blog post, we’ll explore everything you need to know about these powerful valves and why they may be perfect for your industrial application. So let’s dive into the world of knife gate valves!
What is a knife gate valve?
A knife gate valve is a type of industrial valve that controls the flow of liquids or gases through a pipe. It’s called a “knife” gate valve because it uses a sharp-edged disc, known as the “gate,” to cut through and control the flow of material passing through it.
Unlike other valves, knife gate valves are designed specifically for applications where solids and slurry materials need to be tightly controlled. They’re commonly used in industries like mining, wastewater treatment, pulp and paper production, chemical processing, food processing, and more.
Knife gate valves come in different types depending on their design and purpose. Resilient seated knife gate valves have an elastomer seal around the blade while metal-seated ones use metal-to-metal contact to create a tight seal. Uni-directional knives operate with flow only from one direction while bi-directional ones can handle flows from both directions.
These versatile valves are ideal for applications where efficiency is key but they may not be suitable for processes involving high pressure or extreme temperatures.
The different types of knife gate valves
When it comes to selecting a knife gate valve, there are several different types available for various applications. Here’s a breakdown of the different types of knife gate valves:
- Uni-directional Knife Gate Valve: This is the most common type of knife gate valve that only allows flow in one direction. It features a metal seat and requires a minimum pressure drop for closure.
- Bi-Directional Knife Gate Valve: This type of valve can handle flow in both directions, making it ideal for applications where the fluid may reverse its direction.
- Wafer Style Knife Gate Valve: The wafer-style design makes this type of valve less bulky and lighter than other models, reducing installation costs.
- Lugged Knife Gate Valve: A lugged knife gate valve has threaded bolts on each side, allowing them to be installed between flanges without needing nuts or washers.
- Flanged Knife Gate Valves: These valves feature raised face flanges that make it easy to bolt them onto adjoining pipe work or equipment without any welding required.
Ultimately, choosing the right type of knife gate valve will depend on your specific application needs and requirements such as temperature range, pressure rating etcetera..
How do knife gate valves work?
Knife gate valves work by using a sharp-edged blade to cut through and control the flow of materials in a pipeline. The valve has an opening that allows the fluid or material to pass through when it is open, and then closes tightly around the knife for complete shut-off.
The knife gate valve operates with one quick turn of a manual hand wheel or motorized actuator. When turning the handle or actuator, the blade moves up and down from its seat allowing for full closure or complete openness depending on your requirements.
This type of valve commonly used in applications such as slurries, powders, liquids with suspended solids and other heavy-duty industries where conventional valves may not be strong enough to withstand high pressures or abrasive substances.
Unlike other types of valves that use flanges to connect pipes together, knife gate valves are designed with wafer-style configurations which means they take up less space than their counterparts. This makes them ideal for tight spaces where traditional ball valves cannot fit.
In summary, Knife Gate Valves offer excellent performance when handling fluids containing particles like pulp & paper plants effluent streams; wastewater treatment facilities during sludge transfer from primary sedimentation tank etc., thanks to their design which eliminates clogging issues often experienced in conventional metal-seated globe-type control-valves.
The benefits of knife gate valves
Knife gate valves offer a variety of benefits that make them an ideal choice for many industrial applications. One of the biggest advantages is their ability to quickly and effectively shut off flow in pipelines, which can help prevent leaks and spills. This makes them particularly useful in situations where safety is a top concern.
Another benefit of knife gate valves is their simple design, which means they are often less expensive than other types of valves. They also require less maintenance because there are fewer moving parts that can wear out or break down over time.
Knife gate valves are also highly customizable, which means they can be tailored to meet the specific needs of each application. For example, some models come with different types of actuators or stem extensions that allow operators to control flow remotely.
In addition, knife gate valves are excellent at handling viscous fluids like slurries or pastes. Their gates create a tight seal against the valve body when closed, preventing any material from escaping into the surrounding environment.
The benefits of using knife gate valves depend on your specific needs and application requirements. However, these versatile and reliable valves offer plenty of advantages that make them worth considering for many different industries and operations.
The disadvantages of knife gate valves
While knife gate valves have many advantages, they also come with a few disadvantages that should be considered before making the decision to use them.
One potential disadvantage of knife gate valves is their susceptibility to clogging. Because these valves are designed for use with thick fluids and slurries, any solids in the fluid can get stuck in the valve and cause blockages. This can lead to downtime and maintenance costs.
Another drawback is their limited flow capacity. Knife gate valves are typically used for applications with low-to-moderate flow rates, so they may not be suitable for high-volume operations.
Additionally, knife gate valves may not be ideal for handling corrosive or abrasive materials. The soft-seated design of some models can wear down quickly when exposed to harsh chemicals or abrasive particles, leading to leaks and failures.
Because they rely on mechanical force rather than pressure differentials like traditional globe or ball valves, knife gate valves require more effort to operate. This means that larger sizes may require significant force or hydraulic assistance to open and close reliably.
While there are certainly benefits to using a knife gate valve in certain applications, it’s important to weigh these against the potential drawbacks before deciding if this type of valve is right for your needs.
How to choose the right knife gate valve for your needs
Choosing the right knife gate valve can be a challenging task, but with careful consideration of your specific needs and requirements, you can make an informed decision. Here are some factors to consider when selecting a knife gate valve.
Firstly, determine the type of material that will flow through the valve. This is important as it will affect the size and type of valve required. For example, if you’re dealing with abrasive materials such as slurries or granules, you’ll need a heavier-duty valve made from durable materials like stainless steel.
Secondly, think about the operating conditions in which your knife gate valve will operate in. Consider factors like temperature and pressure ratings – these will affect which valves are suitable for use.
Thirdly, take into account environmental factors such as any corrosive agents present in the environment where your system operates. In cases where chemicals or solvents may be involved it’s essential to choose a corrosion-resistant model that can withstand exposure to these elements over time.
Consult industry experts who have extensive experience working with different types of knife gate valves – they’ll be able to guide you on what options are best suited for your unique situation based on their experiences handling similar applications before.
By considering all these crucial aspects regarding choosing a knife gate valve tailored towards meeting individual requirements and preferences becomes less daunting.
Conclusion
To sum it up, knife gate valves are essential components in many industrial applications. They provide a reliable and efficient method of controlling the flow of fluids containing solids or slurry. Whether you need to isolate pipelines or regulate fluid flows, there is always an ideal knife gate valve type suited for your application.
With that said, choosing the right knife gate valve can be quite overwhelming if you’re unfamiliar with its features and specifications. That’s why it’s crucial to work with a reputable supplier who can guide you through the selection process.
All in all, when used appropriately, knife gate valves offer numerous advantages such as tight shutoffs and minimal maintenance requirements while minimizing overall costs associated with downtime and repairs. So take your time to explore these benefits before making any purchasing decisions!