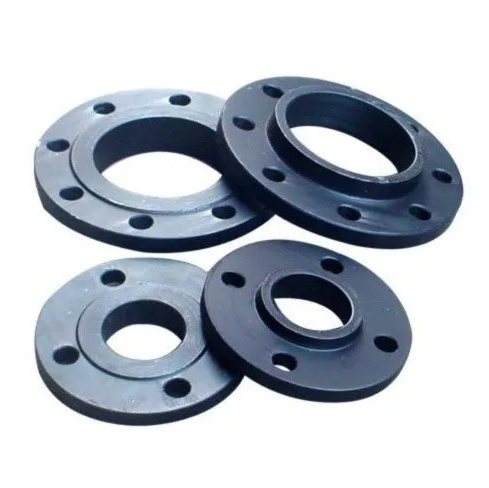
A forged steel flange globe valve is one of the most common materials used in construction. It’s versatile, durable, and more than capable of withstanding the elements. Forged steel flange globe valves are a great example of this. As the world transitions to an increasingly green economy, more and more construction projects are being designed using sustainable materials. One of these sustainable materials is forged steel flange globe valves.
Forged steel flange globe valves are made from a single piece of steel, which makes them stronger and more durable than traditional valve types. They also have a shorter life cycle, meaning they require less maintenance over time. Overall, forged steel flange globe valves are a great choice for green construction projects. If you’re looking for a valve that’s both strong and environmentally friendly, look no further than forged steel flange globe valves.
What is a Forged Steel Flange Globe Valve?
Forged steel flange globe valves are used in many industrial and commercial settings to control fluid flow. They are commonly found in pipelines, water tanks, oil refineries, and other fluid-controlled systems. Forged steel flange globe valves feature a unique design that allows them to open and close quickly. This makes them ideal for controlling large flows of fluid.
Types of Forged Steel Flange Globe Valves
The three most common types of forged steel flange globe valves are ball, butterfly, and orifice. Ball valves are the simplest to design and use, but they can be less efficient than other types of valves. Butterfly valves are more complex to design but offer greater performance than ball valves. Orifice valves have the least number of moving parts and are therefore the most efficient type of valve.
Benefits of Using Forged Steel Flange Globe Valves
In industrial and commercial settings, forged steel flange globe valves offer many benefits over traditional cast iron or brass valves. These valves boast longer life spans, improved flow rates, and resistance to corrosion.
The Benefits of Forged Steel Flange Globe Valves
Compared to other types of valves, forged steel flange globe valves have a number of advantages. They’re more durable, meaning they’ll last longer than cast iron or brass counterparts. This is due in part to their high strength ratings – forged steel can withstand greater forces than other materials without failing. Additionally, forged steel is less likely to corrode, which can negatively affect the performance of a valve.
Another benefit of using forged steel flange globe valves is their ability to handle higher flow rates. This is due in part to the superior design of these valves – they feature finely-machined surfaces that allow for smoother flow. In addition, these valves are often equipped with more robust seals that resist leakage and wear. As a result, these valves are ideal for applications that require high flow rates, such as water pumps and gas turbines.
Advantages of a Forged Steel Flange Globe Valve Over a Cast Iron Globe Valve
A forged steel flange globe valve offers several advantages over a cast iron globe valve. For one, a forged steel flange globe valve is much stronger and more durable than a cast iron globe valve. This strength comes from the fact that the forging process creates a very strong and seamless metal structure. Additionally, forged steel flange globe valves are typically less expensive than cast iron globe valves. Finally, forged steel flange globe valves typically have a longer lifespan than cast iron globe valves due to their superior construction quality.
Disadvantages of a Forged Steel Flange Globe Valve Compared to a Cast Iron Globe Valve
Forged steel flange globe valves are more expensive to produce than cast iron globe valves. Additionally, they may require special machining and welding techniques that can result in increased manufacturing costs. Finally, forged steel flange globe valves may not be as durable as cast iron globe valves.
Applications for Forged Steel Flange Globe Valves
The global market for forged steel flange globe valves is expected to grow at a CAGR of 5.5% from 2016 to 2021, according to a new report by Markets and Markets. The growing popularity of green technology is one key factor driving market growth. Forged steel flange globe valves are considered greener alternatives to traditional brass or bronze valves, as they do not require the use of any metal alloys and are therefore environmentally friendly.
Additionally, for forged steel flange globe valves to function properly, they must be fitted with high-quality seals that are resistant to wear and tear. This is where companies such as ASME come in; they produce quality seals for use with forged steel flange globe valves.
Manufacturing Process for Forged Steel Flange Globe Valves
In order to manufacture forged steel flange globe valves, the necessary raw materials and manufacturing processes must be in place. Raw materials for forging include carbon steel, forgings, fixtures, and tooling. Carbon steel is heated until it reaches a temperature of 1,200 degrees Fahrenheit. The metal is then shaped by pressing and rolling. Forging also creates the necessary fixtures and tooling.
The manufacturing process begins with cutting the carbon steel into the desired shape using a CNC machine or manual labor. The next step is to create the forgings by adding layers of carbon steel until they reach the desired thickness. Then, additional machining is done to create the correct shapes and sizes for the valves. Fixtures are then welded onto the valve body and finally, the finish steps are completed with a coating of Enamel Black Oxide (EBOS).
Market Overview of Forged Steel Flange Globe Valves
The forged steel flange globe valve market is projected to grow at a CAGR of 7.5% during the forecast period 2019-2024. This growth is attributed to factors such as increased demand for recycled products, increasing awareness about the environmental impacts of using traditional valves, and advancements in technology.
The global forged steel flange globe valve market was valued at USD 2.14 billion in 2017 and is expected to reach USD 3.72 billion by 2024, growing at a CAGR of 7.5%. The primary drivers behind this growth are increasing demand for recycled products, increasing awareness about the environmental impacts of using traditional valves, and advancements in technology. The key regions driving the market are North America (USD 1.64 billion), Europe (USD 1.38 billion), Asia Pacific (USD 1.12 billion), and Latin America (USD 0.8 billion).
Some of the major vendors in the global forged steel flange globe valve market are ABB Group (Sweden), Asme (U.S.), Birla Group (India), CNH Global (France), Diebold Incorporated (U.S.), Emerson Electric Co.(U.S.), FANUC Corporation(Japan), General Electric Company(U.S.), Hitachi Corporation(Japan), Huawei Technologies Co., Ltd.(China), Johnson Controls Incorporated(U.S.), KCB Group plc(UK), Larsen & Toubro Limited(India), Mitsubishi Heavy Industries, Ltd.(Japan), National Steel and Engineering Corporation (China), Parker Hannifin Corporation (U.S.), Siemens AG(Germany), ThyssenKrupp AG(Germany), and VALMET Corporation (Finland).
Conclusion
The future of forged steel flange globe valves looks bright. Demand for reliable and durable valves is increasing, which is resulting in manufacturers investing in new forging processes and equipment to meet these demands. This means that the quality of forged steel flange globe valves will only continue to improve, making them an attractive choice for a variety of applications.