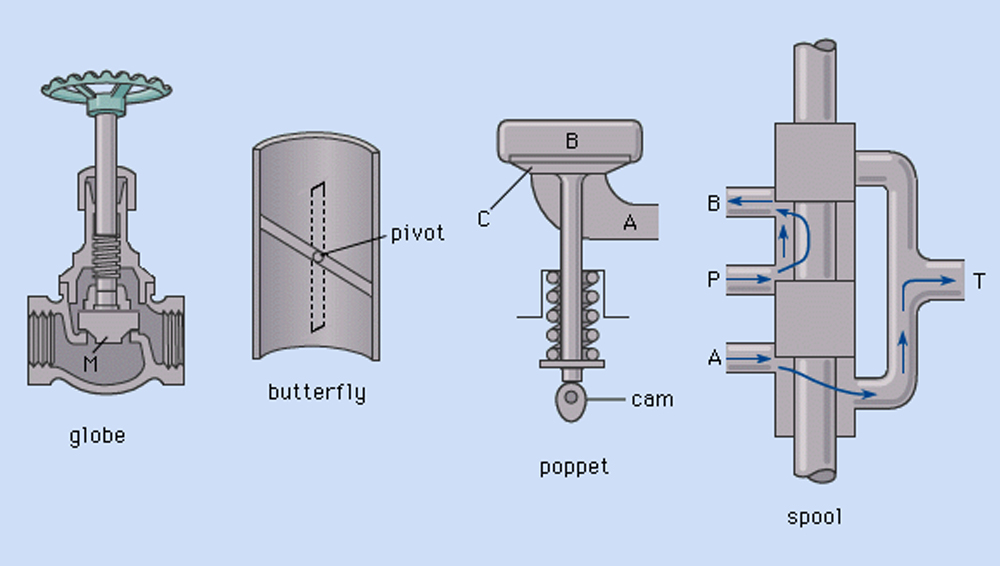
Actuators are electromechanical devices that convert energy into motion. They’re used in a variety of applications, such as robotics, automotive systems, and aerospace. choosing the right actuator for your project is essential to its success.
In this blog post, we’ll explore how to choose an actuator for your project. We’ll cover the different types of actuators, their features, and what to consider when making your selection. By the end of this post, you’ll be equipped with the knowledge you need to choose an actuator that will help you achieve your desired results.
What is an actuator?
An actuator is a device that converts energy into motion. Electric actuators use electricity to produce linear or rotary motion, while pneumatic (air-powered) actuators use compressed air. Hydraulic actuators are powered by liquid pressure and can generate much more force than pneumatic or electric types.
What are the different types of actuators?
An actuator is a device that converts energy into motion. It can be used to control the movement of an object. There are many different types of actuators, each with its own advantages and disadvantages.
Pneumatic actuators use compressed air to generate force. They are often used in applications where high force is required, such as in car brakes. Hydraulic actuators use fluid pressure to generate force. They are often used in construction and manufacturing because they can generate very large forces.
Electrical actuators use electricity to generate force. They are often used in precision applications because they can be very precise and have fast response times. Magnetostrictive actuators use magnetic fields to generate force. They are often used in industrial automation because they are very durable and have a long lifetime.
How do I choose the right actuator for my project?
When choosing an actuator for your project, you need to consider various factors such as the type of application, the force required, the duty cycle, the environment, and the available power supply.
The first step is to identify the application. What will the actuator be used for? Is it a simple on/off operation or does it need to be able to control a machine with precision? Once you know the requirements of the application, you can narrow down your choices.
The next step is to determine the force required. How much weight will the actuator be lifting or moving? What are the static and dynamic loads? Knowing the required force will help you select an actuator with enough power to get the job done.
The duty cycle is another important consideration. How often will the actuator be used? If it will be in continuous use, then you need an industrial-grade actuator that can handle that kind of workload. For periodic or intermittent use, a less robust actuator may suffice.
The environment is also a key factor. Will the actuator be exposed to dust, water, or other harsh conditions? Make sure to choose an actuator that is rated for use in your specific operating environment.
Finally, consider the available power supply. What voltage and current are available? Does your application require AC or DC power? Selecting an actuator that is compatible with your power supply is critical for ensuring safe and reliable operation.
What are some common applications for actuators?
Actuators are used in a wide variety of applications, from simple household tasks like opening and closing doors to more complex industrial processes like moving heavy machinery or controlling the flow of fluids.
In general, actuators convert energy into motion. This can be done using a variety of mechanisms, including hydraulic, pneumatic, or electrical systems.
Each type of actuator has its own advantages and disadvantages, so it’s important to choose the right one for your particular application.
Hydraulic actuators are often used for tasks that require high levels of force, such as moving heavy machinery. They’re also well-suited for applications where precise control is needed, such as in aircraft landing gear systems.
However, they’re not typically used in portable devices because they require a pump to operate.
Pneumatic actuators use compressed air to generate movement. They’re often used in factory automation applications because they’re relatively inexpensive and easy to control.
However, they can’t generate as much force as hydraulic actuators and they’re not well suited for use in explosive environments.
Electrical actuators use electric motors to generate movement. They offer many advantages over other types of actuators, including high efficiency, low maintenance requirements, and the ability to operate in explosive environments.
However, they tend to be more expensive than other types of actuators and can be less reliable in extreme conditions.
Pros and Cons of each type of actuator
There are four main types of actuators: pneumatic, hydraulic, electric, and electromechanical. Each has its own advantages and disadvantages that should be considered when choosing an actuator for a particular project.
Pneumatic actuators are powered by compressed air and are typically the most affordable option. They are also relatively easy to maintain and can be used in a wide range of applications. However, pneumatic actuators can be noisy and may not be as precise as other types of actuators.
Hydraulic actuators use fluid pressure to generate force. They are often more powerful than pneumatic actuators and can be used in high-pressure applications.
However, hydraulic actuators require a pump to generate the necessary pressure, which can add to the overall cost of the system. They also tend to be larger and heavier than other types of actuators.
Electric actuators use electric motors to generate force. They offer a higher degree of precision than pneumatic or hydraulic actuators.
Conclusion
When choosing an actuator for your project, it is important to consider the type of load that the actuator will be required to support.
Pneumatic and hydraulic actuators are best suited for applications where high force output is needed, while electric Linear Actuators are more suitable for lighter loads.
It is also important to choose an actuator that can operate within the temperature range required for your application, as this can vary depending on the type of actuator.
With so many different types and sizes of actuators available on the market, it is important to select one that is best suited for your specific application in order to achieve optimal results.