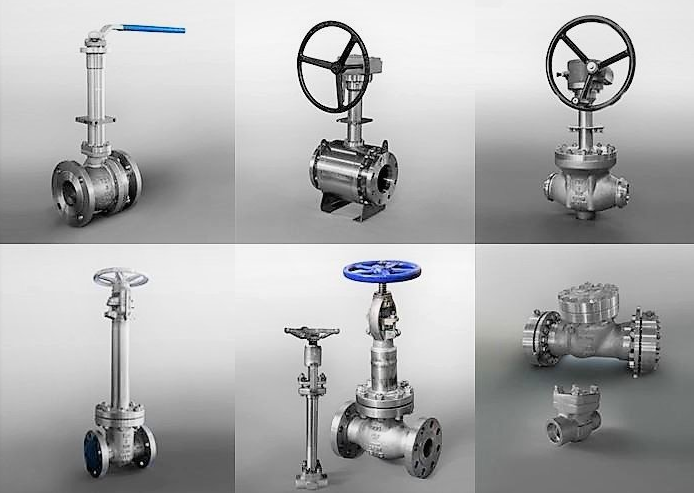
Introduction
When it comes to handling extremely cold substances, there’s no room for error. That’s where cryogenic gate valves come in – these specialized valves can handle the ultra-low temperatures required for industries like aerospace, medical research, and liquefied natural gas (LNG) production. In this blog post, we’ll explore 10 reasons why you need a cryogenic gate valve and how they can make all the difference in your operations. So sit back, grab a warm drink (because let’s face it – we’re not working with cryogenics here!), and read on to learn more about this essential piece of equipment.
What is a Cryogenic Gate Valve?
A cryogenic gate valve is a specialized valve that is designed to control the flow of extremely cold fluids, typically below -150°C. These valves are specifically designed for use in applications where materials must be kept at ultra-low temperatures, such as in liquefied natural gas (LNG) processing plants and cryogenics research facilities.
Unlike conventional gate valves, which are made from materials like carbon steel or stainless steel, cryogenic gate valves are constructed from special alloys that can withstand extreme cold without becoming brittle or cracking. They also feature unique sealing mechanisms that prevent leakage when exposed to very low temperatures.
There are several types of cryogenic gate valves available on the market today, including bolted bonnet, pressure seal bonnet, welded bonnet, bellows-sealed and extended body designs. Each type has its own unique features and benefits depending on the application it will be used for.
Cryogenic gate valves play an important role in keeping industrial processes running smoothly by providing reliable control over fluid flow at ultra-low temperatures. As such, they have become an essential component in many industries where precise temperature control is critical to success.
The Benefits of a Cryogenic Gate Valve
Cryogenic gate valves have numerous benefits that make them a valuable asset in industries dealing with extreme temperatures. Firstly, they are designed to withstand low temperatures and still function correctly. This makes them ideal for use in applications where the fluid or gas being transported is at cryogenic temperatures.
Secondly, cryogenic gate valves have a tight shut-off ability which ensures zero leakage of the fluid or gas being transported. This feature is crucial when handling hazardous substances or processes as it helps prevent accidents and ensures safety.
Thirdly, these valves are highly durable and resistant to wear and tear caused by the extreme cold conditions. They require minimal maintenance which results in reduced downtime for repairs and replacements.
Fourthly, cryogenic gate valves come in various sizes, materials, designs, and configurations which enables their efficient installation across different systems without compromising their performance.
Using cryogenic gate valves can enhance efficiency in many industrial processes as they help regulate flow rates with minimum pressure drop across pipelines due to their high flow capacity design.
The Five Types of Cryogenic Gate Valves
There are five types of cryogenic gate valves that can be used for a variety of applications. Each type has its own advantages and disadvantages, and it’s essential to choose the right one based on the specific needs of your project.
The first type is the bolted bonnet valve, which is commonly used in high-pressure applications. This valve features a threaded cap that allows for easy maintenance and repairs.
The second type is the welded bonnet valve, which offers greater strength than the bolted version. However, it’s also more difficult to repair because the body and bonnet are welded together.
The third type is the pressure seal valve, which provides enhanced sealing capabilities at higher pressures. It’s often used in power plants and other industrial settings where reliability is critical.
The fourth type is known as an extended stem or cryogenic extension valve. This design incorporates a longer stem that extends beyond insulation materials to reduce heat transfer from ambient temperatures outside of piping systems.
There’s the rising stem variant – this design features a visible indication when open or closed while preventing threads from getting damaged by freezing media like liquid nitrogen or helium during operation – ideal for low-temperature service conditions up to minus 196 degrees Celsius (-320 degrees Fahrenheit).
Choosing between these five types requires careful consideration of factors such as operating temperature range, pressure rating requirements as well as maintenance costs over time given their unique designed features.
How to Select the Right Cryogenic Gate Valve
Choosing the right cryogenic gate valve is crucial to ensure its proper functioning and longevity. Firstly, determine the specific application for which you need the valve as this will dictate the material of construction required. The next consideration is temperature range and pressure ratings required for your particular process.
Another important factor to consider when selecting a cryogenic gate valve is its size and end connections compatibility with existing piping systems. You also need to identify if additional features like locking devices, stem extensions or actuation are needed.
It’s vital that you choose a reputable supplier who can provide valves that meet industry standards such as API 600/ISO 10434 for design requirements and ISO 15848-1 or TA-Luft emissions certification for environmental considerations.
Don’t forget about maintenance requirements – select a cryogenic gate valve that has easily replaceable parts in case of wear and tear, reducing downtime during replacement processes.
Selecting the appropriate cryogenic gate valve requires careful consideration of its application needs, material of construction, temperature range & pressure rating compatibility with existing systems, end connections size compatibility & any additional features desired along with choosing from reliable suppliers meeting industry standards while also considering maintenance requirements.
The Different Applications for a Cryogenic Gate Valve
Cryogenic gate valves are used in a variety of applications where low temperatures and high pressures are present. One application is the liquefied natural gas (LNG) industry, where cryogenic gate valves are used to control the flow of LNG from storage tanks during transport.
Another application is in the aerospace industry, where cryogenic gate valves are used to regulate liquid oxygen and hydrogen flows in rocket engines. These valves need to withstand extreme temperature changes during launch and must be able to operate reliably in space.
Cryogenic gate valves also find use in medical research facilities for controlling the flow of liquid nitrogen or other cryogens that are necessary for preserving biological samples or materials. In addition, these valves can be found in laboratories that perform low-temperature experiments or tests.
The food processing industry also makes use of cryogenic gate valves for handling refrigerated gases such as ammonia or carbon dioxide which help maintain optimum temperature conditions within cold storage warehouses.
In summary, there are numerous applications where a cryogenic valve would be required due to its ability to handle extremely low temperatures while maintaining robust functionality.
Conclusion
To sum it up, a cryogenic gate valve is an essential component in any low-temperature system. Its ability to withstand extreme temperatures and prevent leakage makes it crucial for industries such as aerospace, medical, and energy. When selecting the right valve for your needs, consider factors such as pressure ratings, material compatibility, and flow rate.
Investing in a high-quality cryogenic gate valve can save you time, money and reduce the risk of accidents or failure. With so many options available on the market today, finding the perfect one may seem like a daunting task. However, with proper research and professional guidance from experts in this field can help you make an informed decision.
We hope that our article has provided valuable insights into why you need a cryogenic gate valve and how to choose the right one based on your specific requirements. Remember always to prioritize safety when working with low-temperature systems by using reliable equipment that meets industry standards!